Home / News / FRPP Foam Sheet is made by expanding polymers with foaming agents
FRPP Foam Sheet is made by expanding polymers with foaming agents or gas to produce lightweight materials with cushioning, shock-absorbency, thermal insulation, heat retention properties, water resistance, and chemical resistance properties. These types of foam sheets can be easily machined into various shapes for packaging products, furniture, bedding, and toys as well as automotive parts; their eco-friendly biomass-derived ingredients and superior performance properties have made these materials increasingly popular within the industry.
Making flexible FRPP foam sheets involves mixing polypropylene melt with physical blowing agents such as hydrocarbons, chlorinated hydrocarbons, chlorofluorocarbons, and carbon dioxide; along with an isopentane or citric acid-sodium bicarbonate mixture as nucleating agent; at temperatures above its crystallization point but below glass transition temperature; these components are added in an extrusion die to produce continuous sheets of cellular foam which are cured for at least two hours to produce flexible FRPP foam sheets.
At present, it has been demonstrated that flexible FRPP foams made using this method exhibit low rebound properties and excellent acoustic and thermal insulation properties, making these ideal candidates for use as composite applications such as acoustic/thermal/acoustic insulation and lightweight cladding for structures.
The invention produces FRPP foams with excellent compatibility across several resin systems, including polyester, vinyl ester, and epoxy resins. Furthermore, research demonstrates that those produced using an ethylene glycol (EG) core and an epoxy face sheet show superior fire behavior than non-FR PET cores and epoxy face sheets due to interactions between EG and FR in their foam core that influence initial burning phases for sandwich laminates with these characteristics.
6 lb. PIR foam sheets provide excellent thermal insulation and other desirable properties, yet are easily cuttable and bond well with composite materials. However, proper storage and handling guidelines must be observed about this material, along with using appropriate adhesives that ensure compatibility and adhesion between various composite materials.
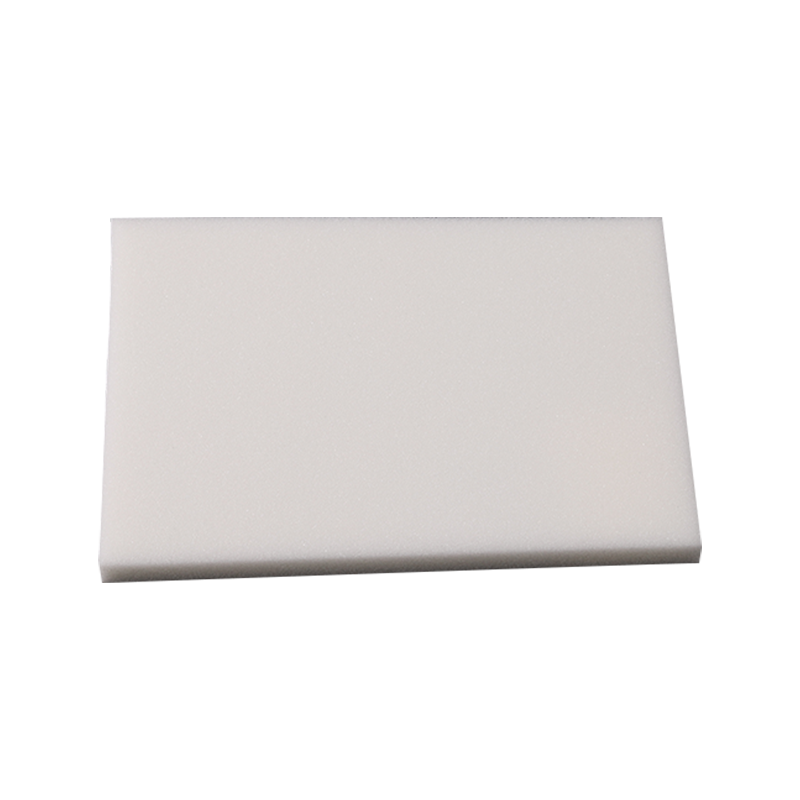