Home / News / Is the production process of FR-MPP Foam Sheet environmentally friendly?
The main raw materials of FR-MPP Foam Sheet usually include polymer matrix, flame retardant and possible reinforcing fillers. The polymer matrix is the main component of FR-MPP Foam Sheet. Common polymer matrices include polyurethane, polystyrene, etc. The production of these polymers often relies on fossil resources such as petroleum, and their extraction and processing will produce certain carbon emissions and energy consumption. Therefore, when selecting a polymer matrix, renewable or bio-based materials should be considered to reduce reliance on fossil resources and lower the carbon footprint. Flame retardant is another key component of FR-MPP Foam Sheet, which is used to improve the flame retardant performance of the material. There are many types of flame retardants, some of which may contain substances that are harmful to the environment and humans. Therefore, when selecting flame retardants, priority should be given to those that are environmentally friendly, low-toxic or non-toxic to reduce potential risks to the environment and human body. Reinforcing fillers such as glass fiber, carbon fiber, etc. may also be used in the production of FR-MPP Foam Sheet to improve its mechanical properties and stability. The acquisition and disposal of these fillers may also have some impact on the environment. Therefore, when selecting reinforcing fillers, you should try to choose environmentally friendly and recyclable materials, and optimize their usage and treatment methods.
During the production process, the manufacturing of FR-MPP Foam Sheet usually includes steps such as batching, mixing, molding and curing. These steps may involve high temperatures, high pressures, and chemical reactions, and therefore require large amounts of energy. Energy consumption not only increases production costs, but may also lead to more carbon emissions. In addition, solvents, catalysts and other auxiliaries used in the production process may cause harm to human health and the environment, such as the emission of volatile organic compounds (VOCs).
Emissions treatment is a key aspect in assessing the environmental friendliness of a production process. In the production of FR-MPP Foam Sheet, the waste gas, waste water and solid waste generated need to be properly treated. Exhaust gas may contain harmful VOCs and other harmful gases, which need to be processed through purification devices to reduce atmospheric pollution. Wastewater treatment is equally important. It is necessary to ensure that harmful substances in wastewater are effectively removed and meet discharge standards. The treatment of solid waste includes recycling and compliant disposal to reduce the occupation of land resources and environmental pollution.
In addition to the environmental impact during the production process, the environmental impact of FR-MPP Foam Sheet itself during use and after disposal is also worthy of attention. As a foam sheet with excellent flame retardant properties, FR-MPP Foam Sheet is widely used in construction, transportation and other fields. However, if the product is not properly maintained and handled during use, it may release harmful substances and cause pollution to the indoor environment. After being discarded, the recycling and disposal of FR-MPP Foam Sheet is also a challenge. At present, the recycling technology and disposal methods for this type of material are not mature enough, which may lead to resource waste and environmental pollution.
With the improvement of environmental awareness and technological advancement, the production process of FR-MPP Foam Sheet is also constantly improved and optimized. In the selection of raw materials, manufacturers are increasingly inclined to use environmentally friendly and renewable materials. For polymer matrices, researchers are exploring the use of bio-based polymers or degradable polymers to replace traditional petroleum-based polymers. These new polymers are derived from renewable resources, such as plant fibers or microbial fermentation products, and therefore have a lower carbon footprint and better environmental compatibility. For the selection of flame retardants and reinforcing fillers, more attention is paid to their environmental friendliness and low toxicity to reduce potential harm to the environment and human body. In terms of production technology, technological innovation makes the production process of FR-MPP Foam Sheet more efficient and environmentally friendly. The application of new energy-saving equipment, such as high-efficiency mixers and low-energy consumption molding machines, not only improves production efficiency, but also significantly reduces energy consumption. By optimizing production process parameters such as temperature, pressure and reaction time, raw material waste and waste generation can be reduced.
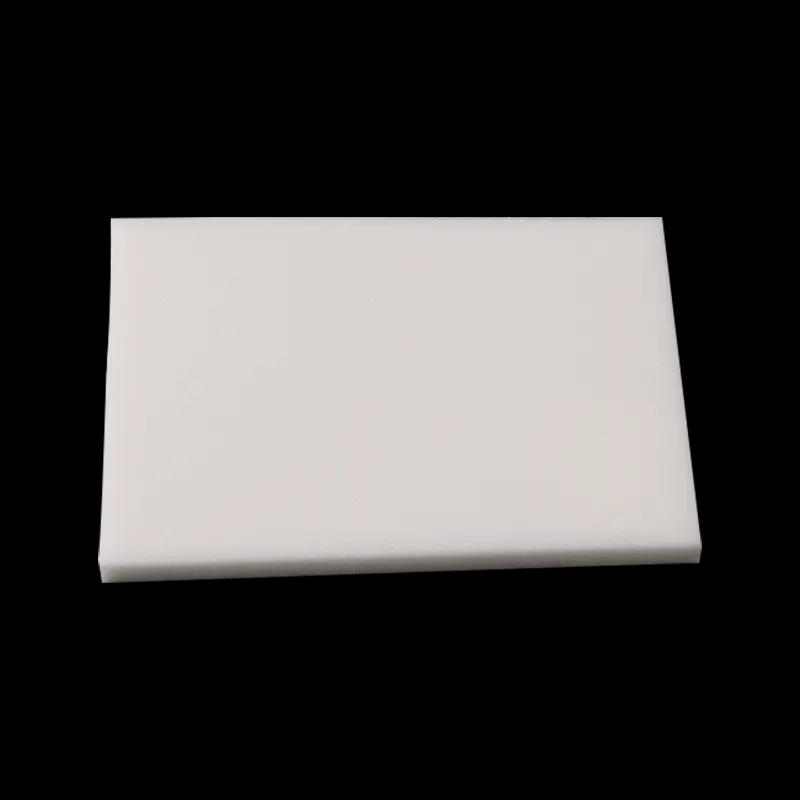