PP Foam Sheet is a lightweight, flexible, and eco-friendly closed-cell foam material. PP is commonly molded into various shapes and sizes for insulation, protection, buoyancy, and packaging applications; manufacturing companies and industrial entities rely heavily on its properties; it has numerous uses across manufacturing and industrial operations due to its unique set of properties; this recyclable material offers excellent shock absorption properties along with thermal & moisture insulation capabilities, strength & durability and can easily be manipulated to form any shape imaginable!
This material is an effective means of absorbing and cushioning impacts from boxes, tools, electronics, or fragile products that need to be shipped directly to customers. Companies using it save on shipping fees while keeping customers' items secure during transit. Furthermore, its UV ray protection makes it suitable for use in areas with thin ozone layers where sun exposure could potentially cause skin or eye damage.
Foam has many applications in the automotive industry, especially car parts. This lightweight yet resilient material makes working with it simple; you can use it to construct everything from door panels and headrests to sun visors and seats - all while cushioning against heat, cold, vibration, etc.
Polypropylene foam can be easily formed into various shapes, making it an excellent material choice for various industrial uses. Depending on its purpose, polypropylene can serve as anti-vibration material in machines and electronics as well as thermal insulation or buoyancy support. Furthermore, its manufacturing process uses minimal energy; thus minimizing environmental impacts during its creation process.
To ensure that materials will produce satisfactory foam sheets, the characterization of polypropylene resin must be properly considered. This includes molecular weight (Mz value), polydispersity index ratios such as Mz/Mw ratios, and molecular weight distribution of resin. If these ranges fall outside acceptable thresholds then unsatisfactory foams with poor cell structure and surface consistency result.
Foam materials that are resistant to ozone must also be considered when selecting them for any application, since exposure to this gas can break down polymers that form part of foams, leading to decreased product quality and foam failure. To mitigate against this issue during the production of polypropylene foam sheets, producers must keep their ozone emissions as low as possible during their process.
To prevent this from occurring, polypropylene resin must be chosen which has high molecular weight and Mz value as well as low polydispersity index values. The Mz/Mw ratio must not be greater than 3.0 while its molecular weight must exceed 1.0x106 to ensure the final foam product resembles pure cellular material as closely as possible.
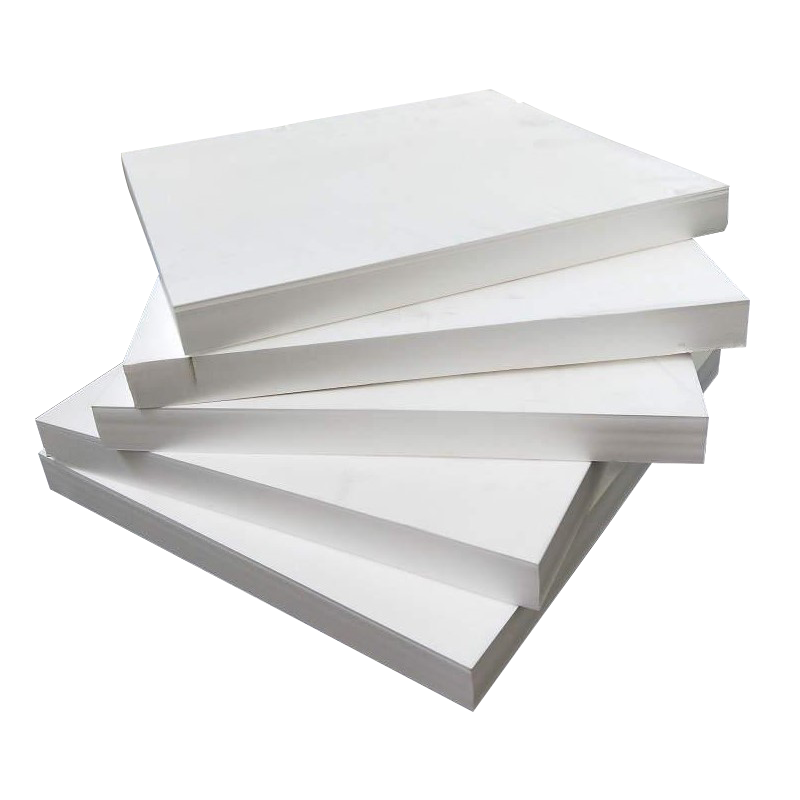
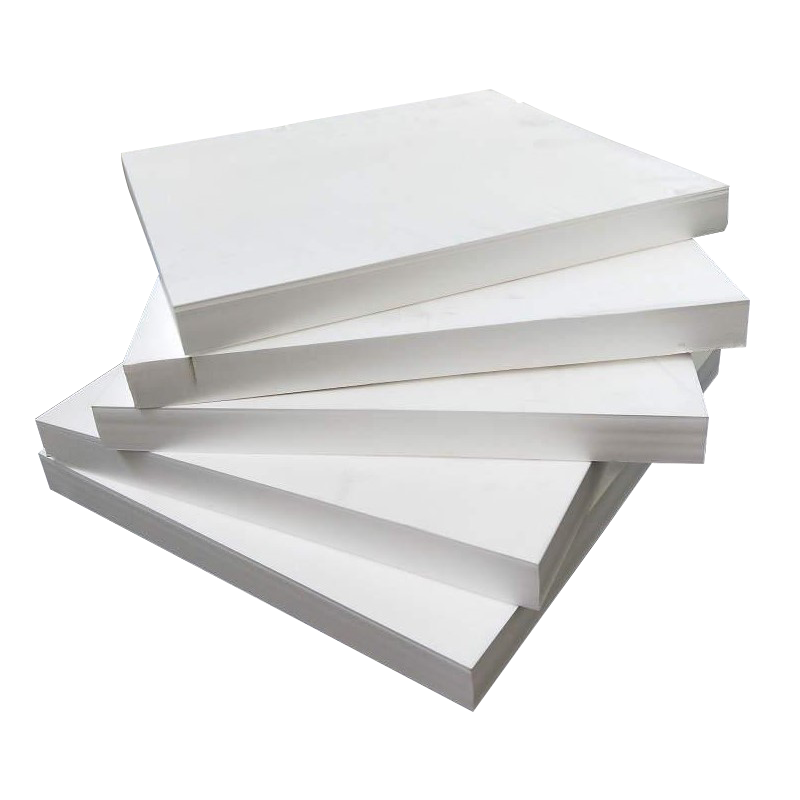