Home / News / PP Foam Sheet is an extremely versatile closed-cell bead foam material with impressive properties
PP Foam Sheet is an extremely versatile closed-cell bead foam material with impressive properties such as energy absorption, multiple impact resistance, thermal insulation, and buoyancy. Furthermore, its lightweight construction, durability, water resistance, and 100% recyclable nature make it highly practical.
Plastic resin is used to craft an extensive array of consumer goods. Its versatility allows it to be easily formed into various shapes, colored, and sealed for storage use in cold storage facilities. Furthermore, its antimicrobial properties make it the ideal material choice when packaging food items as it resists bacteria growth and bacteria regrowth.
PP plastic stands out from other plastics due to its exceptional heat resistance and ability to withstand high temperatures without losing its physical integrity, making it an excellent material for packaging goods that will travel over long distances. Furthermore, its robust structure helps shield items from being damaged during transportation.
EPP is manufactured using polypropylene resin, an extremely versatile substance. This resin can be found across industries from aerospace to automotive manufacturing; from insulation applications such as helping reduce heat losses in production processes to furniture construction; it is both strong and lightweight making EPP an excellent choice.
PP (Polypropylene) is an essential polymer that has numerous applications around the world. As a member of the Acrylonitrile Butadiene Styrene (ABS) family of plastics, this versatile substance can be found in disposable food trays, clamshells, bumpers, and seat backs manufactured with ABS plastic as well as heavy-duty packaging and signage applications.
Extrusion is one of the primary methods used to produce polypropylene foam, using a die to compress a molten mixture of polypropylene and other ingredients into desired shapes, which is then cooled and stabilized before going on for downstream processing.
Production of PS foam requires strict control over its melt temperature distribution and cooling rate to achieve consistent cell structure and quality results. Tandem extrusion lines offer better cellular control than single extruders when applied to this task.
It is possible to produce PS foam using only one extruder, however, this method presents several drawbacks. These include bands or corrugations on the surface of the final cellular foam as well as limited cooling capacities leading to severe gas entrapment and loss.
Problems associated with extrusion also include the appearance of crystalline PP on the surface of finished foams, due to their low melt temperature and cooling rates, which cause its crystals to reorient along gas flow directions, creating uneven skin on their surfaces that cannot be made uniform in appearance.
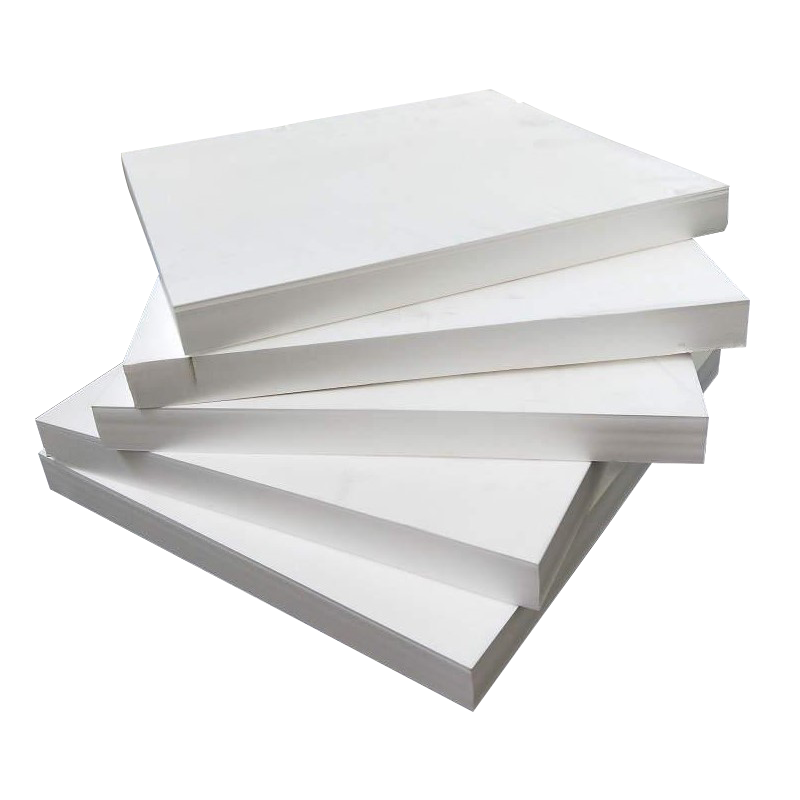